At Sloan Lubrication Systems, we proudly manufacture all of our critical lubrication system components at our factory in Freeport, Pennsylvania. People often ask us, “When there are already so many different lubrication systems on the market, why would you bring your manufacturing in-house?”
There is a very simple reason we did—because uptime matters.
For more than 100 years, we’ve provided our customers with lubrication systems, parts and services. But in the grand scheme of things, what we truly offer is uptime. It’s a promise we make to every customer we serve – that the products we deliver guarantee they will not have unplanned shutdowns. To stand behind that promise, we have to make sure that everything we provide performs and runs flawlessly.
To accomplish this, we focus on two things.
First and foremost – quality. Sloan Lubrication Systems’ customers rely on their critical machinery to operate in extreme environments. To ensure it does, each component of their lubrication system must be perfectly manufactured to deliver long life and reliable performance. Each of these components must go into a system that was optimally designed for the application, and each system must be installed with the highest level of expertise and attention to detail.
Second, and equally important, is availability. All critical wear components need to be available at a moment’s notice to make sure that customers have exactly what they need when they need it, be it a small filter for regular preventative maintenance, a configured divider block to allow a quick change out, or an entire turn-key system to replace a failing one.
When we were working with outside suppliers, we often dealt with long lead times that would delay shipping dates and deliveries to our customers. And in some cases, even if we got the parts, we were disappointed in the quality. We realized that the best way for us to deliver on our promises of quality and availability was to do it ourselves.
And what a great and pivotal decision that has been.

Since we bought our first precision machining center in 2008, Sloan Lubrication Systems has been on a journey of transformation and growth. We moved to a state-of-the-art manufacturing facility in Freeport, Pennsylvania, that more than doubled our square footage. The market responded favorably and within a few years we had to double the size of our facility again.
Gaining total control of our supply chain had some unexpected results as well. Once we started making our own products, we saw ways to make them better. This culture of improvement has continued to fuel our innovation, leading to new ways of doing things and revolutionary products like our TriCip system.
The decision to bring our manufacturing in-house all started with a promise to our customers. And it has been one of the best moves Sloan has ever made. Contact us today and let Sloan help your company with uptime.
Did You Know?
It is easy to prevent check valve failure with proper installation. When a check valve on a high-pressure delivery point is oriented in a way that exposes it to process gas, premature wear and failure will occur. To prevent this, make sure that you orient the tubing so there is always a “wet seat” on the check valve poppet. In cases where this is not possible, we manufacture a gas trap that can be installed after the check valve that has the same effect.
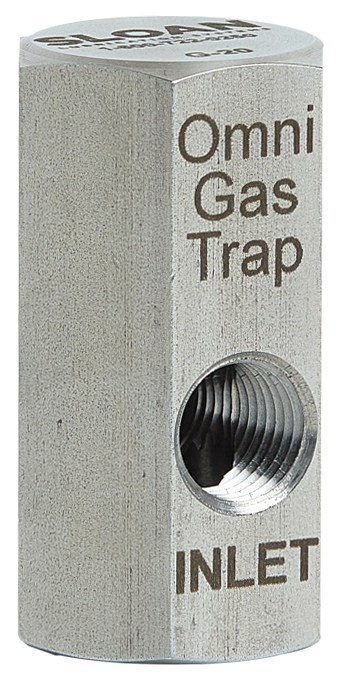